所謂閉模成型工藝就是在陰、陽模閉合的情況下成型復合材料構(gòu)件的工藝方法。SMC、BMC模壓、注射成型、RTM、VEC等等技術(shù)都屬閉模成型工藝。由于環(huán)境法的制定和對產(chǎn)品要求的提高使敞模成型復合材料日益受到限制,促使了閉模成型技術(shù)的應用,近年來尤其促進了RTM技術(shù)的革新和發(fā)展。
RTM是指低粘度樹脂在閉合模具中流動、浸潤增強材料并固化成形的一種工藝技術(shù),屬于復合材料的液體成形或結(jié)構(gòu)液體成形技術(shù)范疇。其具體方法是在設計好的模具中,預先放入經(jīng)合理設計、剪裁或經(jīng)機械化預成形的增強材料,模具需有周邊密封和緊固,并保證樹脂流動順暢;閉模后注入定量樹脂,待樹脂固化后即可脫模得到所期望產(chǎn)品。
這一工藝有著諸多優(yōu)點,可使用多種纖維增強材料和樹脂體系,有極好的制品表面。適用于制造高質(zhì)量復雜形狀的制品,且纖維含量高、成型過程中揮發(fā)成分少、環(huán)境污染少,生產(chǎn)自動化適應性強、投資少、生產(chǎn)效率高。因此,RTM工藝在汽車工業(yè)、航空航天、國防工業(yè)、機械設備、電子產(chǎn)品上得到了廣泛應用。決定RTM產(chǎn)品的首要因素就是模具,由于RTM模具一般采用陰陽模對合方法,因而想辦法提高陰陽模的表面質(zhì)量和尺寸精度就成為決定產(chǎn)品質(zhì)量的一個關(guān)鍵因素。
1)RTM,樹脂傳遞模塑。該技術(shù)源自聚氨酯技術(shù),成型時關(guān)閉模具,向預制件中注入樹脂,玻纖含量低,約20-45%。
2)VARIT,真空輔助樹脂傳遞注塑。該技術(shù)利用真空把樹脂吸入預制件中,同時也可壓入樹脂,真空度約10-28英寸汞柱。
3)VARTM,真空輔助樹脂傳遞注塑。制品孔隙一般較少,玻纖含量可增高。
4)VRTM,真空樹脂傳遞模塑。
5)VIP,真空浸漬法。
6)VIMP,可變浸漬塑法。樹脂借助真空或自重移動,壓實浸漬。
7)TERTM,熱膨脹RTM。在預制件中插入世材,讓樹脂浸漬并對模具與成形品加熱。芯材受熱膨脹,壓實鋪層。利用這種壓實作用,結(jié)合表面加壓成型。
8)RARTM,橡膠輔助RTM。在TERTM方法中不用芯材而用橡膠代之。橡膠模具壓緊成型品,使孔隙大大減少,玻纖含量可高達60-70%。
9)RIRM,樹脂注射循環(huán)模塑。真空與加壓結(jié)合,向多個模具交替注入樹脂,使樹脂循環(huán),直至預制件被充分浸透。
10)CIRTM,Co-Injection
RTM。共注射RTM,可注入幾種不同的樹脂,也可使用幾種預制件,可利用真空袋和柔性表面的模具。
11)RLI,樹脂液體浸(滲)漬。在下模內(nèi)注入樹脂,入入預制件后覆蓋上模,加熱并用熱壓釜的成型壓力成型。加熱使樹脂粘度降低、流動性好,易于浸透。
12)SCRIMPTM西曼復合材料公司權(quán)脂浸漬塑法。申請專利。利用真空袋使樹脂加壓浸漬,浸漬速度快、面積廣。樹脂在預制件的厚度方向也能充分浸漬,必須使用真空袋和軟面模具。
13)UVRTM,紫外線(固化)RTM。與SCRIMP法相似,固化快,必須使用紫外光源,能透過紫外線的真空袋和軟質(zhì)模具。
14)VECTM虛擬設計復合材料VEC的核心技術(shù)是獲得專利的“浮充模具”思想。復合材料對模裝于兩充液的鋼制壓力容器之間,而模具沿容器全長形成密封,容器內(nèi)充滿可壓縮的導熱液體,液體通常為水。
RTM成型工藝流程及工藝特點
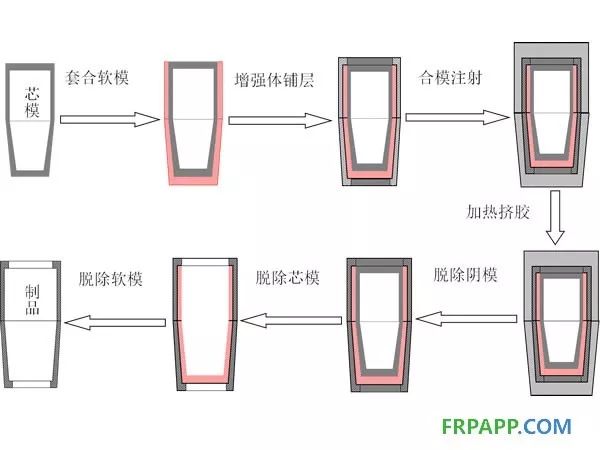
⊙可根據(jù)生產(chǎn)規(guī)模的要求,采用不同材料不同檔次的模具,可最大限度地降低成本,從而獲得較佳經(jīng)濟效益。
⊙屬于閉模樹脂注入方法,可最大程度減少樹脂等有害成分對人體和環(huán)境的毒害,符合環(huán)保要求。
⊙采用低黏度快速固化樹脂,生產(chǎn)過程中可對RTM模具加熱,從而進一步提高生產(chǎn)效率和產(chǎn)品質(zhì)量。
⊙有利于制備大中尺寸、復雜形狀、兩面光潔的整體結(jié)構(gòu)件,尺寸精度好,表面質(zhì)量高,機械性能好。
⊙增強材料預成型體可根據(jù)性能要求進行擇向增強、局部增強、混雜增強及采用預埋及夾芯結(jié)構(gòu),可充分發(fā)揮FRP的性能可設計性。
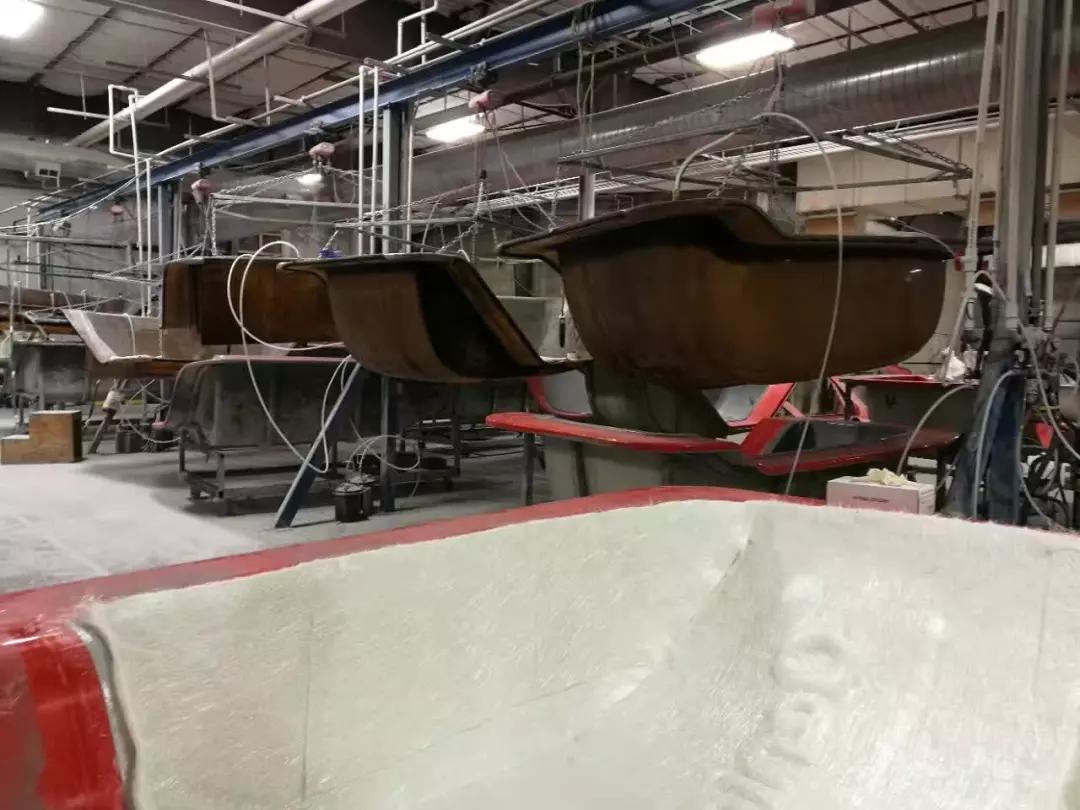
RTM成型工藝模具技術(shù)
1)RTM總工藝路線
RTM有三個重要的組成部分:1原材料系統(tǒng);2注入設備;3模具系統(tǒng)。
2)RTM成型用模具技術(shù)
所有RTM產(chǎn)品都需一適合工藝的模具,RTM也不例外。RTM模具可以用鋁鋼、FRP來制作。由于鋁鋼模具不易變形但價格格高,在這不作介紹。下面主要介紹FRP模具。
1RTM模具型式和材料
FRP模具用于RTM,按一般規(guī)定做——7-10mm厚的模具層板,然后在基礎模具表面下裝入——加熱芯形成夾層結(jié)構(gòu),模具層板總厚為20mm。由于這厚度不能勝任RTM成型工藝所需的強度,因此需進一步增強。箱形鋼型材要比復合材料便宜得多,一般以箱形鋼型材加固。
FRP模具實踐證明用劣質(zhì)樹脂翻制的模具使用壽命極短,而對產(chǎn)品質(zhì)量也有直接影響,所以模具表面要求用耐溫、耐化學腐蝕的材料來做。模具制作成本大部分是人工、材料選擇成本幾乎與模具總造價無關(guān)。目前一般選用乙烯基酯模具樹脂系統(tǒng)和膠衣,并且證明比傳統(tǒng)環(huán)氧材料具有更好的使用壽命和耐溫性。據(jù)國外資料報道,用乙烯基酯模具樹脂制得的模具模塑次數(shù)已超過18000多模次,而且還在繼續(xù)使用。
2模具加熱
用于玻璃鋼工業(yè)的大多數(shù)樹脂都有一與溫度直接相在的固化曲線,所以尋找生產(chǎn)模具能夠控制溫度的方法具有相當?shù)默F(xiàn)實意義,這樣有助于優(yōu)化生產(chǎn)效率。事實上模具溫度每提高10℃,凝膠時間將減半,因此在環(huán)境溫度(20℃)下,模塑一個部件也許固化脫模時間需要60分鐘,而在50℃,同樣的樹脂體系,模塑同一部件,在7.5分鐘內(nèi)就能脫模。
電熱布加熱
在RTM模具中應用加熱布鋪設在模具內(nèi)存的電加熱方式已用了許多年。加熱比較均勻,模具能夠輕而易舉升溫至100℃以上,但標準應用最高模具溫度用到75℃。
液體加熱
液體加熱是將熱循環(huán)和冷循環(huán)系統(tǒng)安裝到合適的模具結(jié)構(gòu)中,可以替代電加熱。這為模具還提供了一個冷卻系統(tǒng)。溫度可通過預埋管子中的循環(huán)介質(zhì)來控制。
3模具的密封
用于RTM和真空模塑(VM)的所有閉合對模都需要一個在模腔邊緣控制樹脂溢流的密封裝置。在VM模塑情況下,需要附加外置模具法蘭真空密封裝置。
密封圈有許多不同的形式,但要求密封圈材料具有耐高溫和一致恢復率。目前看來有機硅膠材用于基本模膠樹脂密封是最成功的。如果用法正確的話,足以提供1000次以上的使用壽命。
被動密封
幾乎專用的固體硅橡膠密封圈截面,設計成當閉模時它的“Z”向末端閉位置可壓縮1.0-1.5mm。要在不提高模具閉模力的情況下達到有效密封,密封圈的硬度和壓縮尺寸的選擇是關(guān)鍵的。只不過因為所需的壓力太大,容易引起模具變形。模具接觸面一般3-5mm足以阻止樹脂滲出,從而達到有效密封!
動態(tài)密封
動態(tài)形式優(yōu)于被動密封形式。它能夠永久地控制截面變化。圖示形式其截面尺寸變化可高達4mm。這使垂直密封軌跡可待嵌入模具法蘭。反之被動密封將僅僅是“塑性變形”并極度磨損。動態(tài)密封圈內(nèi)側(cè)截面一經(jīng)加壓,可提供密封效果很好的調(diào)節(jié)。當模具閉合或啟模時,密封圈隨著真空隙彈性變形,有兒防止了垂直方向的“塑性變形”引起的磨損。
4注射口
搞RTM成型工藝的技術(shù)人員特別重視注射模塑樹脂的入口位置。實踐證明,RTM注射口設在中心位置(視模腔形狀定)是最可靠的。
5模具的精度
RTM模具經(jīng)常處于受力狀態(tài),所以對于成功的閉模模具來說,模具的精度是關(guān)鍵因素之一。模腔精度控制在±0.2mm是閉合模模具的目標精度,達不到該精度將不可避免導致缺膠和不可預見的樹脂充填,并且模塑件尺寸超差。最常見的是超厚,同時要將材料收縮率參數(shù)考慮在內(nèi)。
RTM成型工藝操作及材料選擇
1、RTM工藝操作
RTM工藝注射的操作一般要求在1/4-1/2凝膠時間內(nèi)完成,傳遞時間為2-15分鐘,傳遞壓力為0.3-07Mpa。
樹脂傳遞壓力是RTM工藝中應該控制的主要參數(shù)。此壓力用來克服注入模腔和浸透增強材料時所遇到的阻力。樹脂完成傳遞的時間與系統(tǒng)壓力和溫度有關(guān),時間短可提高生產(chǎn)效率。但如果樹脂流量太大,膠液來不及滲透增強材料,并可以由于系統(tǒng)壓力增加而導致意外。因此,一般要求在傳遞過程中進入模具的樹脂液面上升速度不大于25mm/min。通過觀察排出口來監(jiān)控樹脂傳遞過程。通常以為,模具上所有的觀察口均有膠液溢出并不再排出氣泡,且實際加入的樹脂量與預計加入的樹脂量基本一致時,傳遞過程即已完成。因而排出口設置應周密考慮。
2、樹脂選擇
樹脂系統(tǒng)的選擇是RTM工藝的關(guān)鍵。要將樹脂出至模腔內(nèi)并且使樹脂迅速浸潤纖維其粘度為0.025-0.03Pa•s為最佳。聚酯樹脂粘度較低,常溫下冷注射即可完成。但是,由于產(chǎn)品的性能要求不同,不同類型的樹脂會被選擇,它們的粘度不盡相同,所以管路和注射頭大小均要設計成合適特殊成份的流動性要求。
適合RTM工藝的樹脂有聚酯樹脂、環(huán)氧樹脂、酚醛樹脂、聚酰亞胺樹脂等。
3、增強材料選擇
RTM工藝中增強材料可選用玻璃纖維、石墨纖維、碳纖維、碳化硅和芳綸纖維等。品種可根據(jù)設計需要選擇短切纖維、單向織物、多軸織物、編織、針織、芯材等材料或預成型坯。
RTM制品常見缺陷、原因及解決方法
1、產(chǎn)品表面局部粗糙無光澤
RTM產(chǎn)品產(chǎn)生這種現(xiàn)象的主要原因是產(chǎn)生輕度粘膜。用手在模具上觸摸,當觸摸到這些部位時,手感極其粗糙。通常產(chǎn)品生產(chǎn)一段時間后就會這樣的總題,需要及時清洗模具。首先用水砂打磨模具上粗糙的部位,然后用蘸有丙酮的棉絲擦洗整個模具,最后給模具涂覆脫模劑。
2、起 皺
這是有膠衣制品經(jīng)常發(fā)生的弊病之一。膠衣起皺的的主要原因是在注射樹脂之前,膠衣樹脂固化不完全,注射樹酯中的單體(苯乙烯)部分地融解了膠衣樹酯,引起膨脹,產(chǎn)生皺紋。因此在注射樹脂之前要檢查膠衣是否固化。
3、漏 膠
漏膠的主要原因是模具合模后不嚴密或密封墊不嚴密。合模前檢查密封墊是否完好,有無裂縫等。發(fā)現(xiàn)總是要及時更換。合模時要檢查密封狀況。
4、起 泡
產(chǎn)生這種現(xiàn)象的主要原因1)模腔內(nèi)樹脂固化的應放熱過高,固化時間過短,從而模腔中的氣體沒有完全排出。2)樹脂入模腔時帶入空氣過多,注射時間內(nèi)無法將氣泡完全排出。3)樹脂粘度過大氣泡在注射時不能全部從產(chǎn)品中溢出。4)樹脂注入模腔的壓力過大,致使氣泡包容在樹脂中難以排出。
5、制品內(nèi)部出現(xiàn)干斑
RTM產(chǎn)品內(nèi)部出現(xiàn)干斑主要原因是玻纖浸潤不充分。如果同期產(chǎn)品中出現(xiàn)干斑是某個產(chǎn)品的某個部位,這時也應考慮是否由于玻璃纖維布被子污染造成的。通常制品,內(nèi)部出現(xiàn)干斑也與樹脂粘度有關(guān),所以應首先分析和調(diào)節(jié)樹脂粘度。查看模具流道是否太長或太窄,及時修改模具。查看給料管,改進給料管,改進給料管,增加給料點
6、芯材移動
注射時芯材的移動是由于流動的不穩(wěn)定性引起的,可通過在芯材上開孔來解決或確保加在芯材上的閉合壓力遠大于該處樹脂的壓力,增強材料的移動,如纖維的沖刷也是由于合模壓力相對于注射壓力不足。